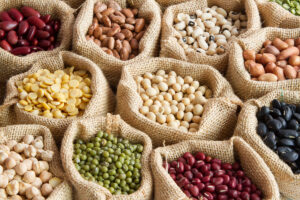
Most corporate food safety policies today call for detecting foreign objects in food products after packaging. That way consumer safety can be completely assured. This however, in some industries where contaminants may be prevalent as a result of agriculture, can create costly hand sorting, scrap and even missed shipment commitments.
So bulk X-ray inspection to detect metallic and non-metallic contaminants prior to packaging or shipment for further processing is gaining in popularity. The design of these X-ray machines is also a straightforward extension of package X-ray with new considerations given to X-ray safety, cleaning and minimization of rejected material. Some of the food processors starting to adopt bulk X-ray are in the nut, seed, fruit and vegetable sectors.
X-ray inspection adds value by augmenting other sorting techniques
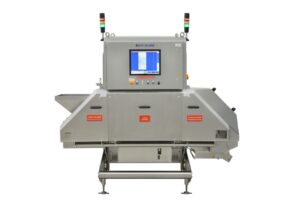
(product flow from top left to right)
For many years bulk food processors relied on magnets, sieves, gravity and metal detectors to screen out foreign objects from the fields and picking processes. These approaches were hit or miss and usually could only detect large, primarily metal, objects. For this reason, more precise high speed optical sorters became popular, they could find things that looked different than the food products. Sorters are very expensive though and can be “fooled” when a contaminant is similar in appearance to the food product or hidden under a too thick layer. Because of this, and the need to meet higher and higher customer standards, food processors started investigating the use of X-ray inspection at the end of the line. But were they able to catch the small, subtle and usually non-metallic objects the other systems missed?
The results were surprisingly good, enabling the highest quality processors to make faster, cleaner shipments to their customers saving time and money.
Understanding the basic elements of a bulk X-ray system
There are six main elements of bulk X-ray inspection systems that should be understood and evaluated prior to selecting the ideal solution.
- Inspection width and X-ray power
- Infeed hopper design and flexibility
- Product metering device
- Inspection tunnel design including guiderails
- X-ray inspection software
- Multilane rejection system
Determining the system inspection width and X-ray power needed is the first consideration. CASSEL Inspection offers three models with inspection widths varying from 250 to 450 mm (each with a slightly wider belt). It is typical to run a product height on the belt of 20-30 mm (a single layer or only some layers of product put one over another), but performance will vary depending on belt speed and product density. Generally speaking, as the X-ray beam widens to maximize throughput the system will need higher X-ray power. For example, the CASSEL XD45-H1-BULK model incorporates a 480W X-ray source. In the end the best way to determine the important specifications of inspection width and X-ray power is to do a complete application/throughput review with the X-ray supplier.
Next, the infeed design should be evaluated to assure your product flow can be easily transitioned from a conveyor or tube into the X-ray machine. The XD45-H1-BULK hopper was designed to be fed from any direction, but if issues arise CASSEL Inspection can also customize the infeed to meet your needs.
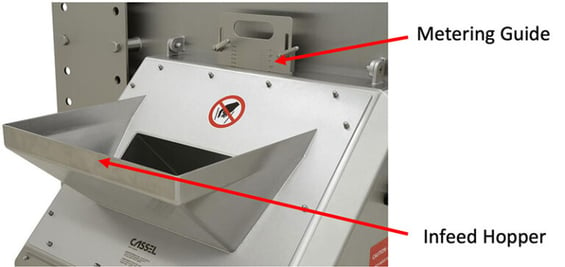
Because X-ray inspection is most reliable when there is a consistent density of product, bulk X-ray machines must have a product metering device, usually a sliding gate. During installation a technician determines the ideal product height for a given belt speed and the gate is set accordingly. The range of adjustment should be from 10-100 mm to cover a broad set of applications.
Once a consistent flow of product is in the inspection tunnel, guiderails keep it on the belt and within the beam width as it passes through the X-ray beam. X-ray image “strips” are continually processed by the machines software to detect and reject foreign objects. All doors to access this area must have safety interlocks and care must be given to X-ray shielding to assure X-rays do not scatter out the infeed or rejection areas. To make cleaning and belt replacement easy removal of the guides and belt should be tool less.
Because contaminants can be dense, sharp and hidden amongst several layers of product, multiple image processing algorithms should be used to make a detection. The CASSEL XIA X-ray software comes with over 40 algorithms to inspect almost any product. In the bulk inspection application contrast changes due to local density changes are typically evaluated and filtered by their size and/or shape to eliminate of false detections.
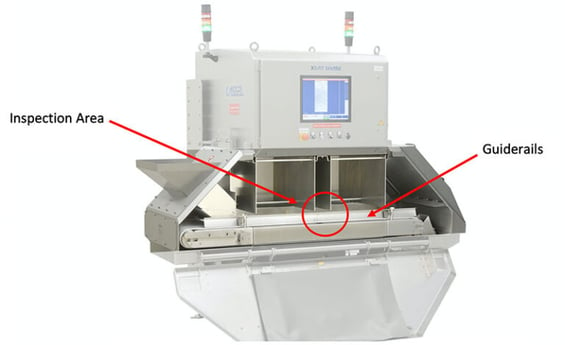
Finally, to minimize scrap and waste, the system should inspect product in multiple lanes with a product diverter that only rejects a portion of the belt when a contaminant is located. Mechanical gates can be used are 75-100mm wide and for even tighter control air jets are possible reducing the reject width down to <10 mm in some cases.
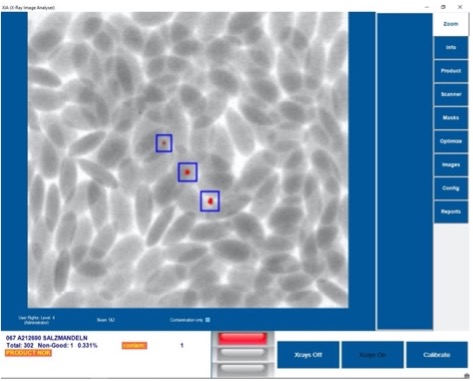
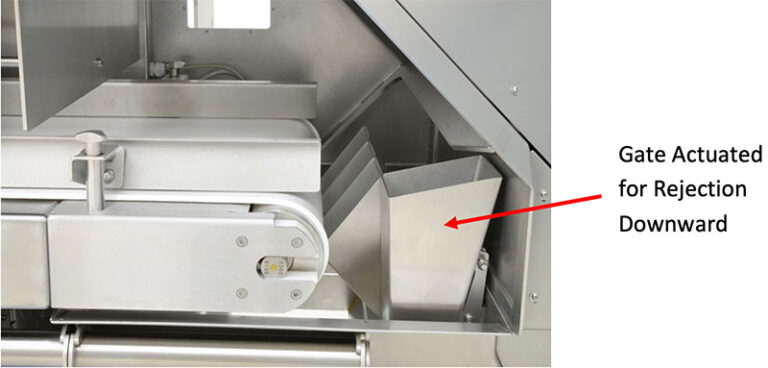
Understanding detection performance and tradeoffs
No two bulk X-ray applications are the same. To explain the range of performance possible we will use an example of almonds. Almonds have a bulk density around 0.55 kg/l and a single almond is about 6mm tall when lying flat on the belt. What types and sizes of contaminants can be detected in various layers of almonds at typical throughput rates?
To illustrate this real-world application, we will use the XD45-H1-BULK system which has a maximum inspection width of 446 mm. We will run the belt at a moderate 46 m/min speed. Refer to the table below to see the ranges of detection depending on product height (and machine throughput). Stainless steel detection is the easiest/best and does not vary by product height, but detection of other non-metallic materials is more difficult and can vary with product thickness. Please note most metals aside from aluminum have density similar to stainless steel so their detection is very good too.
Using this inspection width, belt speed and a reasonable product thickness (from 24 to 36 mm) on the belt assures the throughput can easily meet this industry’s requirements.
Layer Height | Throughput | Stainless Steel Ball | Soda Lime Glass Ball | Stainless Steel Wire Diameter (2mm long) | Ceramic Ball | Aluminum Ball |
Two layers (12 mm) | 8100 kg/hr | 1.2 mm | 2.5 mm | 0.8 mm | 2.5 mm | 3.0 mm |
Four layers (24 mm) | 16200 kg/hr | 1.2 mm | 2.5 mm | 0.8 mm | 3.0 mm | 4.0 mm |
Six layers (36 mm) | 24300 kg/hr | 1.2 mm | 3.0 mm | 0.8 mm | 4.0 mm | 5.0 mm |
Eight layers (48 mm) | 32400 kg/hr | 1.2 mm | 3.5 mm | 0.8 mm | 5.0 mm | 5.0 mm |
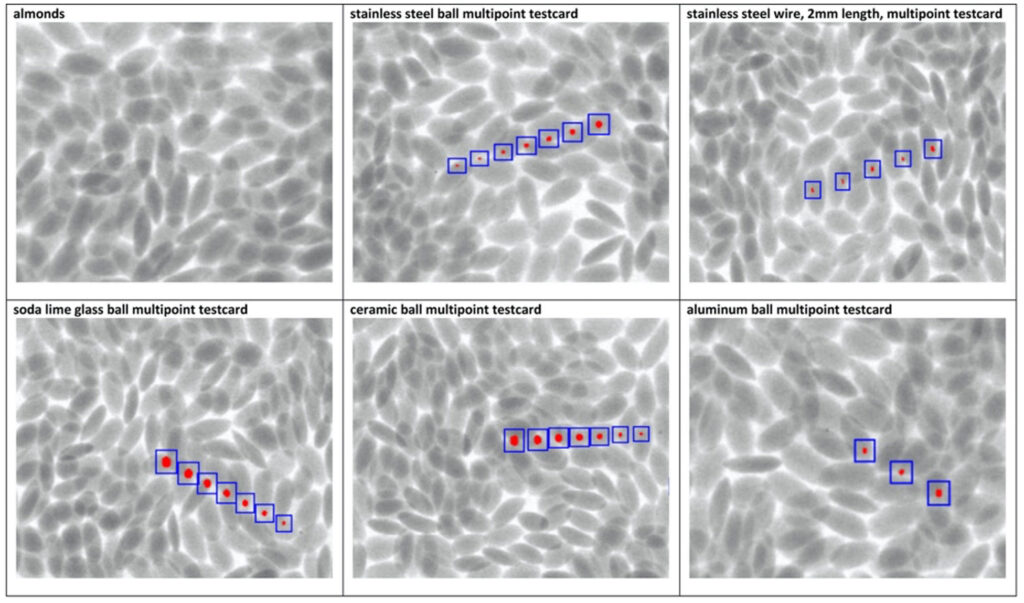
A few things should be noted regarding this example:
- The maximum X-ray power of the XD45-H1-BULK (80 kV/6 mA or 480W) assures the product height does not have to be too low or the belt speed too slow limiting throughput.
- X-ray power is automatically adjusted so that it penetrates the product but does not saturate the detector impacting detection of less dense materials.
- Less dense products with lower throughput requirements could be run on the smaller XD25-L1-BULK and XD35-L1-BULK models with less power.
This is only an example of one application on one size of X-ray machine. CASSEL Inspection engineers can work with you on your application to fit and test the best machine for your purposes.
Seeing is believing
In the past decade X-ray inspection has penetrated a broad range of packaged product applications and is the fastest growing product inspection segment. Bulk X-ray inspection, however, is just starting to be applied in a range of applications so its utility is not fully understood and appreciated. The primary driver for bulk X-ray is that older screening and sorting methods may no longer be sufficient to supply the highest quality, clean product to your customers. In many cases X-ray can detect foreign objects these technologies may miss.
No matter what product you process, CASSEL Inspection can design an inspection system that meets all of your needs. The CASSEL Inspection team can perform a full application evaluation presenting the levels of detection and throughput you could expect. They can also describe in detail the many unique design details of the XD Bulk machines making them easy to use, maintain and service. Why not upgrade from your older inspection methods to a new, state-of-the-art X-ray inspection machine? Contact CASSEL Inspection today to learn more about how we can protect your product, your equipment, and your customers.