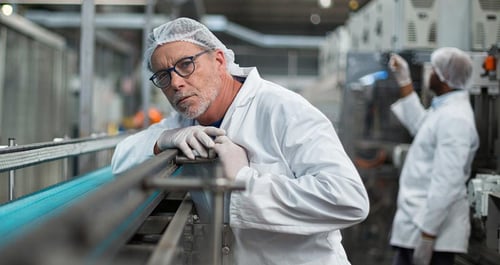
Kontaktieren Sie uns!
Tel. (+49) 5502 91150
info@cassel-inspection.com
Metalldetektoren als Teil der Qualitätssicherung
Ein Metalldetektor spürt metallische Fremdkörper in nicht-metallischen Produkten auf und wird in vielen industriellen Produktionsprozessen eingesetzt. Gerade die Lebensmittelproduktion stellt hohe Anforderungen an Produktqualität und Hygiene.
Aufgabe des Metalldetektors
Mein Metalldetektor sorgt für:
- Reinheit der Rohstoffe – Wareneingangskontrolle
Wer seine Rohstoffe präzise überprüfen kann, ist in der Lage, durch Früherkennung die Fehlerkosten zu reduzieren und Lieferanten zu bewerten.
- Reinheit des Fertigprodukts – Warenendkontrolle
Der Kunde darf nur reine, metallfreie Produkte erhalten. Der Grad der Metallfreiheit muss dabei immer so hoch sein, wie er technisch realisierbar ist.
- Absicherung der Produktionseinrichtungen – Prozesskontrolle
Produktionseinrichtungen können durch eingeschleuste Metallteile empflindlich gestört, beschädigt oder sogar zerstört werden. Maschinen- und Anlagenstillstände haben negative Auswirkungen auf die Konstanz der Produktqualität und die Produktionsmenge.
- HACCP – Kritischer Kontrollpunkt (Metallfremdkörper)
Ein kritischer Kontrollpunkt ist ein Punkt innerhalb der Produktionskette, an dem eine fehlende Überwachung ein nicht zu akzeptierendes Gesundheitsrisiko darstellt.
Funktionsweise von Metalldetektoren
Metalldetektoren arbeiten nach einem induktiven Messprinzip. Von einer Senderspule wird ein hochfrequentes, elektromagnetisches Wechselfeld erzeugt. Bewegt sich ein Metallteil durch den Metalldetektor, erfährt dieses Feld eine Änderung, die den magnetischen und elektrischen Eignschaften des Metallteils entspricht.
Die Feldänderung wird von einem abgeglichenen Empfägerspulenpaar registriert und anschließend in der Elektronik aufbereitet und digital ausgewertet
Dieses Messprinzip reagiert auf elektrische Leitfähigkeit und Magnetismus und erkennt damit alle Metallarten, also auch Buntmetalle (z.B. Aluminium oder Messing) und Edelstahl. Allerdings lassen sich magnetische Metalle etwas besser erkennen als unmagnetische. Das Messfeld durchdringt die geprüften Lebensmittel und erkennt Metallteilchen auch im Produktinneren oder in Verpackungen.
Die Lebensmittel selbst werden durch die Messung in keiner Weise beeinträchtigt oder verändert.
Technische Grenzen
Die maximale Empfindlichkeit wird durch die dem Messprinzip zugrundeliegenden, physikalischen Gesetze begrenzt.
Lebensmittel besitzen oft eine mehr oder weniger starke elektrische Leitfähigkeit durch Salz-, Zucker-, Mineralien- und Wasseranteile.
In der Praxis ist die erreichbare Empfindlichkeit hauptsächlich davon abhängig, wie gut der Metalldetektor diese Produkteffekte kompensieren kann.
Klassische Metallsuchsysteme
- Metallsuchband: In ein Förderband ist ein Metalldetektor integriert, der den Fördergurt rahmenförmig umschließt oder als Fläche darunter angebracht ist. Es stehen verschiedene Methoden zur Verfügung, erkannte Metallteilchen auszusondern (z.B. Pusher).
- Fallrohr: Riesenfähiges Material fällt in einer Rohrleitung durch rahmen- oder ringförmige Metalldetektoren. Erkannte Metallteilchen werden mit einer Separierklappe ausgesondert.
- Inline-Detektor als Bestandteil einer Rohrförderanlage: Dieses Inlinesystem dient zum Aufspüren von Metallteilchen in pastösen oder flüssigen Produkten und wird in die Förderleitung integriert (z.B. mit einer Milchrohrverschraubung). Mit Metall verunreinigte Produktteile werden über spezielle Ventile ausgeschleust.
Einbauort
Es können sowohl verpackte als auch unverpackte Produkte auf Metall untersucht werden. Die Überprüfung der bereits verpackten Waren ist meistens zu bevorzugen, weil eine erneute Verunreinigung mit Metall zu diesem Zeitpunkt nahezu unmöglich ist. Unverpackte Ware nimmt aber manchmal deutlich weniger Raum ein – es kann also ein deutlich kleinerer Metalldetektor eingesetzt werden. Dieser kann u.U. auch deutlich kleinere Metallteile aufspüren.
Unverpackte Ware oder verpackte Ware, die sich nicht sinnvoll überwachen lässt (z.B. wegen metallhaltiger Verpackung oder zu großer Verpackungsabmessungen) sollte zusätzlich geprüft werden. Wird ein Metalldetektor in erster Linie zur Maschinenabsicherung eingesetzt, sollte der Einbau möglichst dicht vor der zu schützenden Maschine erfolgen.
Empfindlichkeit und Zuverlässigkeit
Grundlage für eine optimale Empfindlichkeit ist die richtige Wahl der Suchspule. Die Größe der Suchspule muss den Produkteigenschaften angepasst sein. Als Faustregel gilt in den meisten Anwendungen: Je kleiner der Metalldetektor, desto höher die Empfindlichkeit.
Die optimale Empfindlichkeit ist dann erreicht, wenn der Metalldetektor di kleinstmögliche Prüfkugel erkennt, ohne dass dies zu Fehlauslösungen aufgrund äußerer Einflüsse oder durch Schwankungen in den Produkteigenschaften führt.
Höchste Priorität hat, dass der Metalldetektor zuverlässig und ohne Fehlauslösungen arbeitet.
Änderungen der Detektoreinstellungen dürfen nur von eingewiesenem Personal druchgeführt werden. Jede Änderung sollte dokumentiert werden, damit jederzeit Klarheit über den aktuellen Betriebszustand herrscht.
Testverfahren und Testintervalle
Mit Hilfe von metallischen Prüfkugeln in definierten Größen wird die Funktion des Metalldetektors im Betrieb getestet. Dem Produkt wird eine Prüfkügel beigegeben und beides zusammen durch die Suchspule gefahren. Wenn die Kugel dabei vom Detektor erkannt wird, ist er einsatzbereit.
Die Testintervalle müssen sol festgelegt sein, dass bei Feststellung einer Unregelmäßigkeit alle Produkte nochmals überprüft werden können, die seit dem letzten Test den Metalldetektor durchlaufen haben. Außerdem sollte ein Test zu jedem Schichtbeginn und bei jedem Produktwechsel durchgeführt werden.
Dokumentation
Die Metallüberwachung muss in einem nach HACCP oder ISO 9000 arbeitenden Betrieb schriftlich dukomentiert werden. Damit wird die Metallüberwachung nachvollziehbar und gegenüber Prüfstellen oder im Audit belegbar.
Eine lückelose automatische Dokumentation der Metallerkennung, der Tests sowie aller eingestellten Parameter erfolgt über digitale Schnittstellen oder ggf. zusätzlich eine Protokolldrucker.
Ursachenforschung und Kennzeichnung metallhaltiger Produkte
Wird im Laufe der Produktion ein Metallteil detektiert, muss unbedingt nach dessen Herkunft geforscht werden. Die Ursache muss konsequent beseitigt werden, damit weitere Verunreinigungen aus derselben Quelle ausgeschlossen werden können.
Es muss unbedingt sichergestellt werden, das als metallhaltig erkannte Produkte nicht versehentlich wieder verwendet oder an Kunden ausgeliefert werden. Diese Produkte müssen also entsprechendd deutlich gekennzeichnet sein, z.B. mit einem roten Aufkleber mit der Aufschrift „Gesperrt – Metall!“.
Wartung
Ein moderner Metalldetektor ist mit einer automatischen Selbstkontrolle ausgerüstet und im Grunde wartungsfrei.
Vorbeugende Wartung durch den Detektorhersteller bedeutet Beratung und Prüfung vor Ort, ob das gerät nach längerem Betrieb noch korrekt installiert ist. Es wird untersucht, ob externe Störeinflüsse vorliegen könnten und ob die Suchempfindlichkeit für aktuelle Produkte und den aktuellen Standort noch optimal ist. Dazu gehört außerdem die Schulung und Einweisung neuer Mitarbeiter sowie die Integration des Metalldetektors in das betriebliche Qualitätsmanagement.
Produkthaftungsgesetz
Bereits seit dem 01.01.1990 haften Lebensmittelhersteller ungeachtet eines Verschuldens für Schäden, die ihr fehlerhaftes Produkt verursacht. Dies kann zu erheblichen Kosten für Rückrufaktionen oder sogar gerichtliche Verfahren führen.
HACCP
HACCP (Hazard Analysis and Critical Control Points = Risikoanalyse und kritische Kontrollpunkte) ist ein Fehlerverhütungskonzept für die Lebensmittelindustrie.
Für die Metallerkennung fordert HACCP:
- Der Metalldetektor ist ein kritischer „physikalischer“ Kontrollpunkt gegen die Gefahr einer Metallverunreinigung, denn es ist wahrscheinlich, dass beim Verlust der Kontrolle ein gesundheitsrisiko für den Endkunden entsteht.
- Der kritische Grenzwert für die Eichung auf die kleinste zu erkennende Metallprüfkugel ist die Nachweisbarkeit. Ein Produkt muss so frei von Metall sein, wie durch „Good Manufacturing Practice“ (GMP) und nach dem neuesten Stand der Technik möglich ist. Bezogen auf den Metalldetektor bedeutet das: Es sollen alle Metallteilchen aus dem Produkt entfernt werden, die ein moderner Metalldetektor bei optimaler Installation gerade noch zuverlässig aufspüren kann.
- Der kritische Grenzwert muss auf jeden Fall so festgelegt sein, dass der Metalldetektor stabil, zuverlässig und ohne Fehlalarm arbeitet.
- Es muss sichergestellt werden, dass alle Produkte durch den Metalldetektor geprüft werden.
- Der Betrieb und die Ergebnisse des Metalldetektors müssen vollständig dokumentiert werden..
- Korrekturmaßnahmen nach einer Metallerkennung: siehe Ursachenforschung.
- Vorbeugende Wartung: siehe Wartung.
DIN ISO 9000
Es ist empfehlenswert, für das Metallsuchgerät eine betriebliche Arbeitsanweisung zu erstellen, die z.B. die Maßnahmen nach einer Metallerkennung und das regelmäßige Testverfahren festlegt. Eine Muster-Arbeitsanweisung ist bei CASSEL Inspection auf Anfrage verfügbar. Alle unter HACCP genannten Punkte gelten auch für ISO 9000.
Lebensmittelhygiene-Verordnung
Die EU-Richtlinie über Lebensmittelhygiene 93/43/EG verpflichtet Lebensmittelhersteller, ein auf Grundlage des HACCP-Systems fußendes Eigenkontrollsystem einzurichten. Ein Metalldetektor wird in der Richtlinie nicht explizit gefordert, jedoch beinhalten die HACCP-Grundsätze unter anderem die Kontrolle von physikalischen Gefahren wie z.B. Metallfremdkörpern.
Die o.g. Richtlinie ist mit der Lebensmittelhygiene-Verordnung (LMHV) vom 05. August 1997 in deutsche Recht übernommen worden. Lebensmittelbetriebe werden zur Durchführung von betriebseigenen Kontrollmaßnahmen auf der Grundlage der in §4 Abs.1 LMHV aufgeführten fünf Grundsätze des HACCP-Konzeptes verpflichtet. Es wird – auch unter Produkthaftungsgesichtspunkten – dringend empfohlen, die Durchführung der Eingenkontrolle zu dokumentieren.